Hard Truths at 8,400 RPM: The Unvarnished Art of Running and Maintaining High-Speed Centrifugal Separators
The first time the Alfa Laval separator powered up beneath me, it was 3am. The engine room vibrated with anticipation—and a gnawing sense of doubt. Manuals in hand, I realized no page could teach you the smell of a scorched bearing or the rattling pulse that signals impending chaos. This isn’t just about following a checklist—it's about becoming part detective, part craftsman, and part philosopher, with the machine as both partner and puzzle. If you’ve ever stared down a 134 kg spinning bowl wondering, ‘Did I tighten that right?’, then this post is for you.
Thinking Like a Separator: The Operator’s Mental Toolkit
Operating a high-speed centrifugal separator at 8,400 RPM is not just about following a checklist. It’s about developing a mental toolkit that blends technical knowledge, intuition, and disciplined routines. Manuals provide the foundation, but the real art of running and maintaining these machines comes from understanding their inner workings and responding to subtle cues that only experience can teach.
Visualizing the Separator’s Inner Flow
A skilled operator doesn’t see the separator as a black box. Instead, they visualize the journey of bilge water as it enters the bowl, is spun at incredible speeds, and separates into oil, clean water, and sludge. At 8,400 r/min, the forces inside are immense. Oil, being lighter, migrates inward, while water and sludge are flung outward. This mental model helps operators anticipate where issues might arise—whether it’s a clogged disc stack or a misaligned gravity disc. When separation quality drops, the operator can mentally trace the flow and reason through possible causes, instead of relying on guesswork.
Intuition: The First Line of Troubleshooting
Troubleshooting a separator is as much about intuition as it is about technical skill. Manuals can list symptoms and possible faults, but they can’t teach the feel of a machine that’s running “off.” Operators learn to spot subtle vibrations, hear a change in the machine’s hum, or even notice the faint smell of overheated grease. These early warning signs often appear long before alarms sound. As one marine supervisor put it, “A manual can’t replicate the subtle change in hum that tells you trouble is brewing long before the vibration alarm goes off.” Research shows that early detection of abnormal vibration or temperature can prevent catastrophic failures and reduce downtime.
Routine: Documentation and Baselines
Routine is not just about habit—it’s about building a reliable record. Operators who log every maintenance action, vibration reading, and operational anomaly create a valuable history. Setting baselines, such as noting that normal vibration is 9 mm/s, allows for quick identification of deviations. Service logs are more than paperwork; they are a living memory for the machine, especially important during crew changes or when troubleshooting recurring issues. Studies indicate that disciplined documentation is key to maintaining warranty, ensuring safety, and optimizing service intervals.
Log operational parameters: Throughput, temperature, and vibration should be recorded regularly.
Document every service: Include date, running hours, replaced parts, and any unusual findings.
Track lessons learned: Note what worked and what didn’t during troubleshooting or maintenance.
Quality Over Speed: The True Cost of Rushing
There is a strong temptation to rush maintenance, especially when under pressure to get the separator back online. However, experience shows that taking shortcuts often leads to greater problems. A hurried job can result in misaligned parts, missed warning signs, or even safety hazards. As echoed in the field, “Do it right, or do it twice.” The five extra minutes spent cleaning a component or double-checking an O-ring can mean the difference between smooth sailing and a midnight disaster. Research underscores that quality-focused maintenance reduces unplanned downtime and extends equipment life.
In the world of high-speed separators, the operator’s mental toolkit—visualization, intuition, routine, and a focus on quality—forms the backbone of safe and efficient operation. Manuals provide the rules, but it’s these unwritten habits that keep the heart of the engine room beating strong.
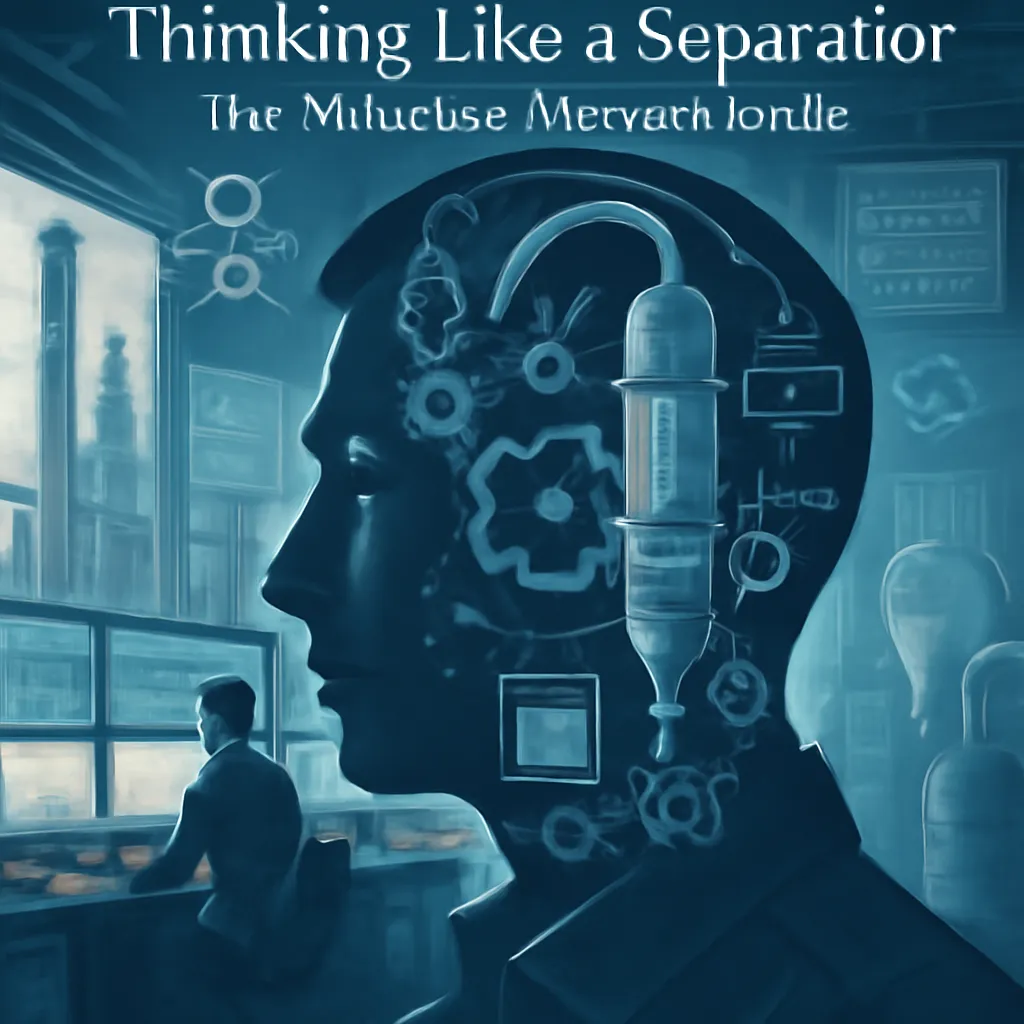
When Manuals Meet Reality: Inspection, Safety, and Those ‘Oh No’ Moments
There’s a certain comfort in the crisp, authoritative pages of an equipment manual. For high-speed centrifugal separators like the Alfa Laval BWPX 307TGD-71, the manual is precise: top bearing every 8,000 hours, friction coupling checks, and a strict sequence for every operation. But as any marine engineer with years in the engine room will tell you, the real world rarely lines up so neatly. Manuals are essential, but they can’t capture the subtle signals or the gut-check moments that define real-world maintenance and safety.
The 8,000-Hour Rule—and Why You Don’t Wait for the Alarm
According to the manual, the top bearing should be renewed every 8,000 hours. It’s a clear, non-negotiable line in the sand. Yet, field wisdom often whispers a different story: don’t wait for the alarm, don’t trust that everything is fine just because the hours haven’t ticked over. Research shows that preventive maintenance, not reactive intervention, is what keeps these machines running safely and efficiently. A bearing can start to fail long before it triggers a vibration warning or an unbalance alarm. Those who have spent long nights at sea know that a subtle change in the machine’s hum or a faint uptick in vibration can be the first sign of trouble—one that the manual can’t always prepare you for.
Safety Protocols: No Room for Complacency
The separator’s bowl weighs 134 kg and spins at 8,400 r/min. The kinetic energy stored in that mass is immense—enough to turn a minor oversight into a catastrophic event. Manuals are filled with warnings, but in practice, it’s easy to become complacent, especially after hundreds of uneventful start-ups. The reality is stark: safety protocols aren’t suggestions. Studies indicate that most serious incidents occur when operators cut corners, ignore lock-out procedures, or bypass safety interlocks. The consequences can be fatal, not just for the operator but for anyone nearby. Every checklist, every interlock, every “wait until the bowl stops” rule exists because someone, somewhere, learned the hard way.
Unbalance Sensors: Between Gentle Warning and Emergency Stop
Modern separators are equipped with unbalance sensors—a thin line between a gentle nudge and a full-blown emergency stop. The manual sets the warning at 1V (0.3mm) and the trip at 2V (0.6mm). In theory, these thresholds are clear. In practice, the sensor’s readings can drift, and the difference between a minor vibration and a dangerous one isn’t always obvious. Operators quickly learn to respect these numbers, but also to listen for the subtle cues that precede them: a change in the machine’s tone, a vibration that feels different underfoot. Ignoring these early signals, or dismissing a warning as a “false alarm,” is a gamble that rarely pays off. As one seasoned engineer put it, “The separator always gives you a warning—you just have to be paying attention.”
Oddball Failures: The O-Ring That Stole a Week
Not every failure is dramatic. Sometimes, it’s the smallest part—a simple O-ring in the paring chamber—that brings everything to a halt. Manuals list O-rings as routine spares, but they rarely capture the frustration of tracing a persistent leak to a single, overlooked seal. One faulty O-ring can mean a week’s stay in port, lost time, and mounting pressure from above. These are the “oh no” moments that manuals can’t predict, but every experienced operator remembers. They’re a reminder that, in the world of high-speed separators, the devil is always in the details.
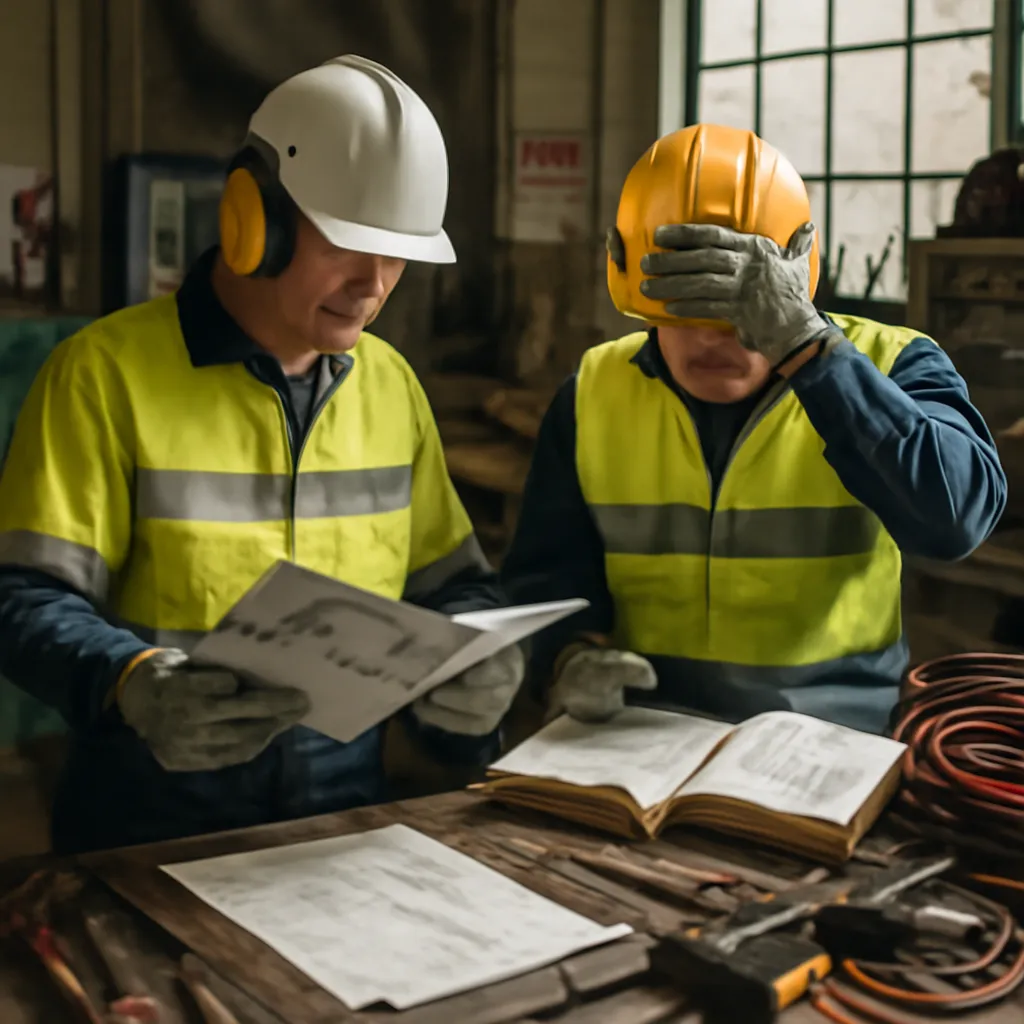
Spare Parts, Service Kits, and the Art of Not Running Out at Sea
There’s a certain gamble that comes with managing spare parts inventory on a vessel. The temptation is always there: cut back on inventory, save a bit on upfront costs, and hope nothing goes wrong. But when a high-speed centrifugal separator like the Alfa Laval BWPX 307TGD-71 is involved, that gamble can turn into a logistical nightmare. Picture this: a flat belt fails mid-ocean, and the only replacement is sitting in a supplier’s warehouse, ten days away by courier. The separator is down, the captain is furious, and the cost of downtime quickly dwarfs any savings made by trimming the spares budget.
Research shows that the most effective maintenance strategies for separators are built on a foundation of preparation and foresight. This means not just following the manufacturer’s maintenance schedule, but also ensuring that the right parts are always within arm’s reach. The official manuals are clear: periodic dismantling, cleaning, and inspection are non-negotiable, and each of these steps relies on having the correct service kits and spare parts on hand. Without them, even a minor issue can escalate into a major operational headache.
Essential Spares: What Every Ship Should Carry
The core of any robust inventory is the service kit. For the BWPX 307TGD-71, this means both the Intermediate Service (IS) and Major Service (MS) kits. These kits contain all the seals, gaskets, and wear parts needed for scheduled maintenance—items that are guaranteed to be needed, not just “nice to have.” Alongside these, certain high-wear items deserve special attention:
Flat belts: These are designed to wear out and will fail eventually. Having a spare on board is essential.
Friction blocks: Another consumable that can bring operations to a halt if not replaced on schedule.
Key O-rings: Especially the bowl hood seal, which is notorious for causing leaks if it fails.
Optional sensors: Speed and unbalance sensors are less likely to fail, but when they do, the separator is offline until a replacement arrives.
Service logs and spare parts catalogues are not just bureaucratic paperwork; they are critical tools for tracking usage and anticipating needs. Studies indicate that ships with disciplined inventory management and regular service logging experience fewer unplanned outages and lower overall maintenance costs.
The Myth of Non-Genuine Parts
There’s a persistent myth that non-genuine parts can save money without consequence. In reality, only Alfa Laval genuine spares are manufactured to the exact tolerances and material specifications required for safe, reliable operation. Using non-genuine parts not only risks premature failure but can also void the system’s warranty. As the manuals and safety instructions repeatedly emphasize, system integrity and crew safety depend on using the right components.
“Myth: Non-genuine parts save money. Fact: Only Alfa Laval spares maintain system integrity and warranty.”
When a $12 O-Ring Becomes the Most Expensive Part on the Ship
Sometimes, the smallest oversight can have the biggest impact. There’s a well-worn story among marine engineers: a $12 O-ring wasn’t stocked because it seemed trivial. When it failed, the separator was out of action for days, resulting in $18,000 in lost charter time. That O-ring instantly became the most expensive part ever purchased—or, more accurately, not purchased. It’s a lesson that’s been repeated in countless engine rooms: the true cost of a spare part is measured not by its price tag, but by the consequences of its absence.
Ultimately, the art of not running out at sea is about more than just having a well-stocked storeroom. It’s about understanding the real-world stakes of separator maintenance, respecting the lessons learned by those who have faced the consequences, and making inventory decisions that prioritize operational resilience over short-term savings.
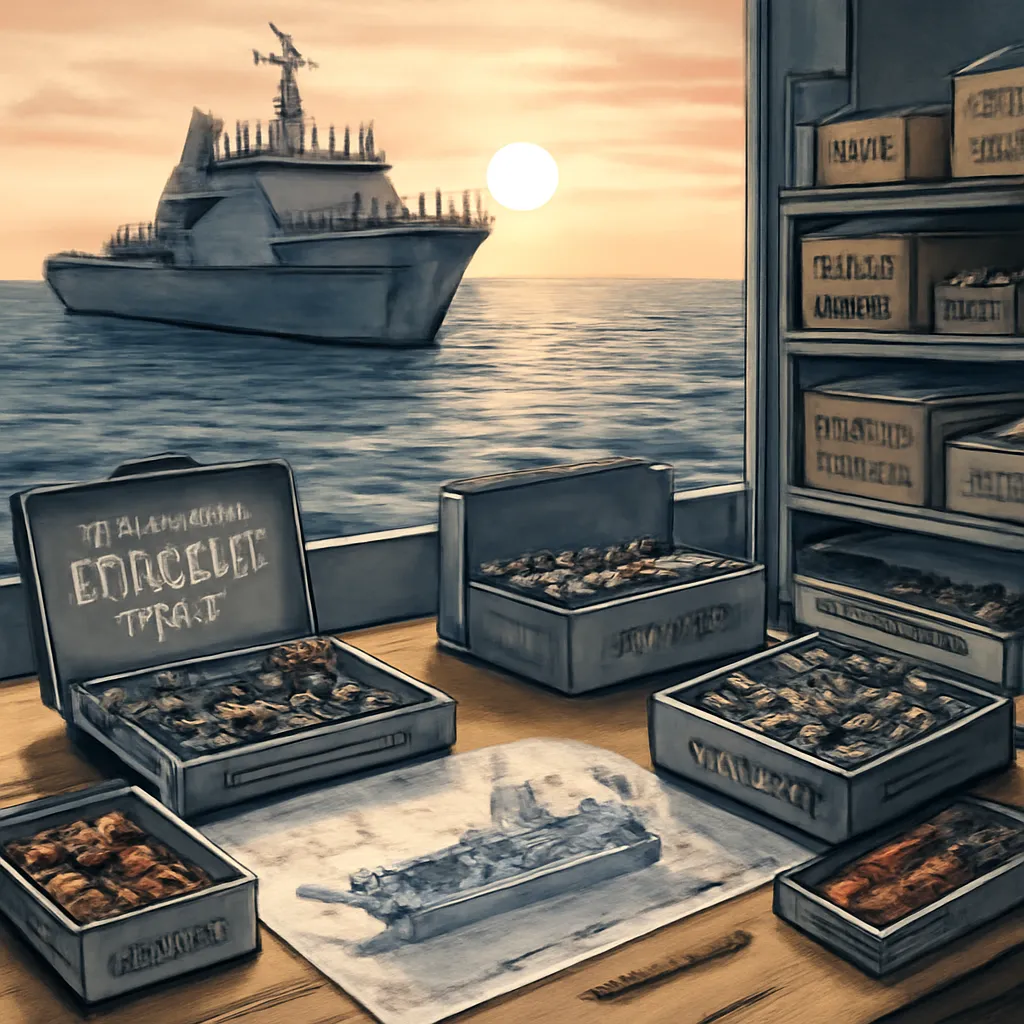
Preventive Mindset vs. Reactive Regrets: Scheduling, Training, and Always Learning
The Mindset Divide: Fix-It-When-It-Breaks vs. Service-So-Nothing-Breaks
In the world of high-speed centrifugal separators, the mindset an engineer brings to the job often shapes the fate of the machinery. There’s a clear divide between those who wait for something to break before acting and those who work to ensure nothing breaks in the first place. Research shows that preventive maintenance, when prioritized, leads to fewer catastrophic failures and lower long-term costs. Yet, the “if it ain’t broke, don’t fix it” mentality still lingers, especially among less experienced crew. The question is: which mindset are junior engineers inheriting from their mentors?
A seasoned supervisor might say, “You can teach procedures, but you can’t teach attitude.” Manuals outline every step, but they can’t instill the habit of checking vibration logs or listening for subtle changes in the separator’s hum. The difference is subtle but critical. One approach waits for alarms; the other listens for whispers.
When to Overhaul: Syncing Service with Port Stays vs. Accumulating Maintenance Debt
Strategic maintenance scheduling is more than just following the manufacturer’s intervals. It’s about aligning major overhauls—like the 8,000-hour service—with planned port stays, not squeezing them in at the last minute or, worse, deferring them indefinitely. Studies indicate that every deferred service adds to what’s often called “maintenance debt.” This debt isn’t just theoretical; it collects interest in the form of increased wear, higher risk of failure, and, eventually, emergency repairs at sea.
The reality is that a separator doesn’t care about a vessel’s schedule. It will demand attention when its components reach their limits. The smart move is to anticipate, plan, and execute overhauls during controlled downtime. Otherwise, the cost of an unplanned breakdown—lost time, regulatory headaches, and expensive logistics—can far exceed the price of a timely service.
Operator Training: The Three-Pillar Approach
Competence in separator operation is built on three pillars: manual study, mentoring, and live drills. First, the instruction manual is the foundation. Operators must know it inside out, from safety warnings to troubleshooting charts. But as many supervisors will admit, “The book can’t teach you what a real alarm sounds like at 3 a.m.”
Manual Study: Understanding procedures, safety protocols, and technical data.
Mentoring: Learning from experienced engineers who have faced real-world failures and successes.
Live Drills: Practicing emergency stops, responding to alarms, and running through fault scenarios in real time.
Research highlights that hands-on training, especially with real alarms and simulated failures, is essential for developing operational intuition. It’s one thing to read about a high-vibration shutdown; it’s another to react calmly when the separator starts to shake and the alarms blare.
A Wild Card Exercise: The Separator as a Chessboard
Imagine your separator as a chessboard. Every move—every maintenance decision, every skipped inspection, every parameter adjustment—sets the stage for the next. Miss a step, and the consequences may not be immediate, but they will come. Each overlooked vibration reading or delayed service is like leaving a piece undefended. Eventually, the board tips in favor of failure.
This mental exercise isn’t just a metaphor. It’s a reminder that in separator operation, every action (or inaction) has a ripple effect. The best operators think several moves ahead, anticipating problems and setting up for success long before the alarms sound.
“Experience is paid for with long nights, greasy hands, and the occasional, humbling failure.” — Marine Engineering Supervisor
A preventive mindset, strategic scheduling, robust training, and systems thinking—these are the moves that keep the separator, and the ship, running strong.
Beyond the Manual: Fine-Tuning, Emergency Response, and Building Vendor Partnerships
Running a high-speed centrifugal separator like the Alfa Laval BWPX 307TGD-71 is never just about following the manual. Manuals are essential, but the reality of operating at 8,400 RPM is far more nuanced. The real art lies in the details—those subtle adjustments, the practiced responses to emergencies, and the relationships built over years of shared experience. Research shows that the most reliable and efficient operations come from blending technical knowledge with field-tested intuition and a willingness to learn from every cycle.
First, there is no such thing as “set and forget.” Every batch, every feedstock, every environmental change can shift the optimal settings. Feed temperature, discharge interval, and throughput are not static numbers—they are variables that demand attention. Over-optimizing for efficiency, such as stretching discharge intervals to save water, can backfire. A separator bowl overloaded with compacted sludge risks not just poor separation, but also dangerous unbalance and shutdowns. As one seasoned marine engineer put it, “The separator will punish you for shortcuts. It rewards only careful, continuous tuning.” Studies indicate that a disciplined approach to parameter adjustment, guided by both data and observation, is key to maintaining both performance and safety.
Emergency response is another area where manuals provide the framework, but experience fills in the gaps. When the unbalance sensor suddenly blares at 2V (0.6mm), it’s not just a technical event—it’s a test of preparation. Imagine a midnight scenario: alarms sound, the machine vibrates, and the instinct is to act fast. But what comes next? The best crews have drilled for this. They know the protocol: hit the emergency stop, evacuate, and never restart until the root cause is found. Research underscores the importance of regular emergency drills and clear, posted procedures. In the heat of the moment, muscle memory and practiced routines prevent panic and protect both people and equipment.
Building a smart data culture is often overlooked, but it’s fundamental. Logbooks and digital records are only as valuable as the attention paid to them. Patterns in vibration readings or gradual changes in start-up times can reveal issues long before alarms trigger. Yet, too often, these records are filed away and forgotten. The real value comes when operators and supervisors actively review logs, look for trends, and act on early warnings. As one industry guideline notes, “Service logs are essential for tracking maintenance and ensuring proper service intervals and procedures.” A culture that encourages curiosity and follow-up turns raw data into actionable insight.
Finally, there’s a “wild card” that separates good operations from great ones: treating your vendor as a partner. Too many see the manufacturer as just a call center for parts or complaints. But the engineers who get the most out of their separators are those who build relationships with vendor reps, share operational stories, and swap troubleshooting tips over coffee. These informal exchanges often yield practical solutions and insider knowledge that never make it into official documentation. As one veteran engineer recalled, “I learned more in an hour with an Alfa Laval tech than I did in a week of reading manuals.” Studies and field reports confirm that proactive vendor partnerships can lead to faster problem resolution and more effective preventive maintenance.
In the end, the unvarnished art of running and maintaining high-speed centrifugal separators is about going beyond the manual. It’s about fine-tuning, preparing for the unexpected, making data meaningful, and building human connections. These are the lessons that keep the heart of the engine room beating strong—batch after batch, voyage after voyage.
TL;DR: The journey to separator mastery isn’t just in following manuals—but in seasoned judgment, continuous learning, and proactive action. Safety, strategy, and skilled execution turn routine tasks into lasting reliability.
Comments
Post a Comment