Behind the Wrench: Lessons from the Chief Mechanic’s Chair on LNG Ship Maintenance, Safety, and Team Brilliance
Ever find yourself diagnosing a fuel pump issue in the middle of the South China Sea, with a storm brewing, and the VeM scheduled to call for an operational update? Welcome to a day in the life of a Chief Mechanic on an LNG carrier. From juggling maintenance logs to quelling team nerves when the alarm klaxon blares, I’ve learned that operational excellence is equal parts science, art, and, frankly, luck. But there’s nothing quite like the buzz of restoring full propulsion after an engine hiccup—except maybe the satisfaction of a team that trusts your lead. Today, I’m pulling back the curtain on the real stories, surprises, and lessons that define safe and stellar LNG ship operations.
Maintenance and Repair Requirements: The Unseen Backbone of LNG Ship Safety
Daily, Weekly, and Voyage-Specific Maintenance Tasks
The operational safety and efficiency of LNG vessels depend on a disciplined approach to maintenance. Each day, engineering teams conduct routine checks on propulsion systems, generators, pumps, and cargo handling equipment. Daily tasks often include monitoring fluid levels, inspecting for leaks, and ensuring critical alarms and sensors are functional. Weekly routines expand to more detailed inspections—checking the integrity of pipework, verifying the calibration of safety devices, and cleaning air filters. Voyage-specific maintenance is planned around operational demands and anticipated port calls, with teams preparing for increased system loads or environmental changes.
Research shows that preventative maintenance and scheduled inspections are essential for early detection of wear and tear, helping to avoid costly breakdowns and ensuring compliance with international safety standards. As one Chief Mechanic noted in a recent case study, “The backbone of LNG ship safety isn’t just the technology—it’s the discipline of sticking to the maintenance schedule, no matter what the clock says.”
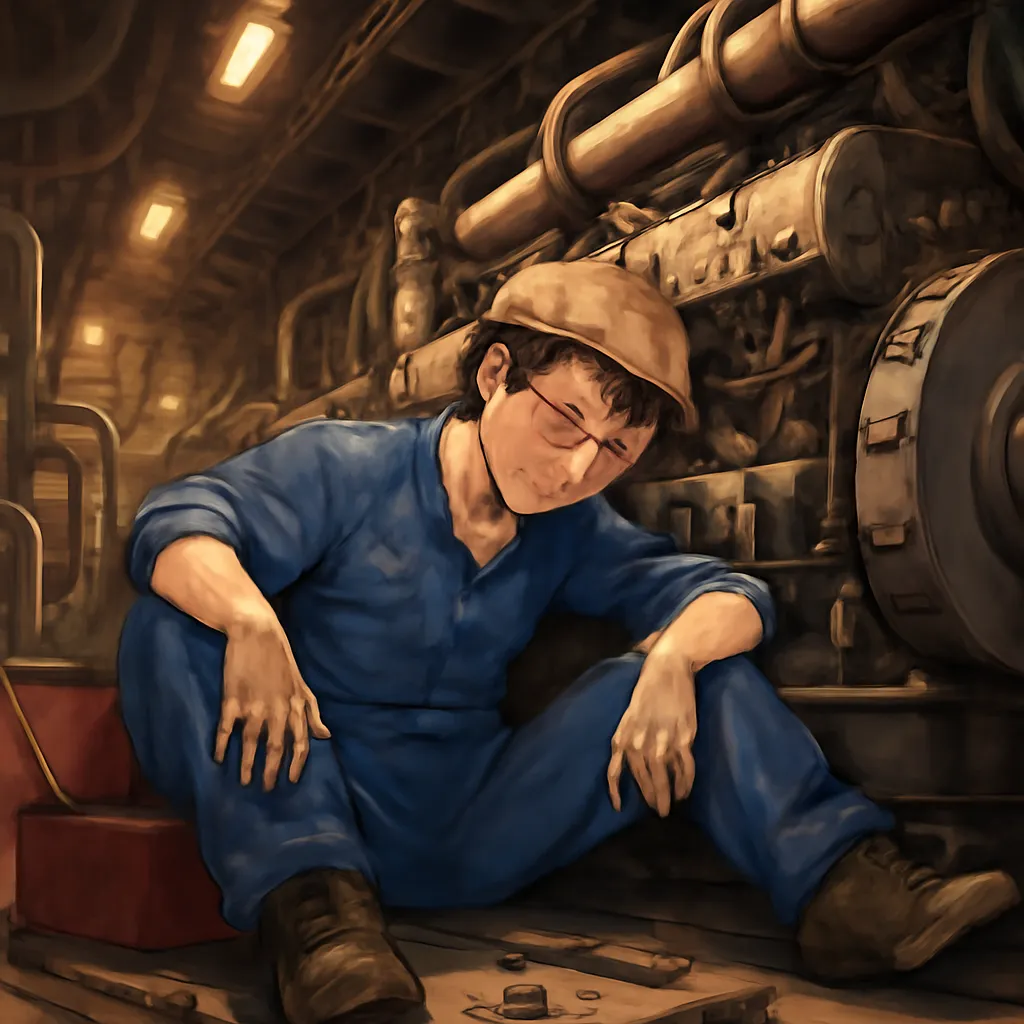
Personal Anecdote: The Midnight Lubrication Dash
There are moments when the routine becomes urgent. One such instance, recounted by a Chief Mechanic, involved a “midnight lubrication dash” just hours before entering a busy port. A vibration alarm had triggered in the main engine room, hinting at possible bearing stress. Despite the late hour, the engineering team sprang into action—donning protective gear, gathering tools, and moving quickly but methodically. The team’s focus was on lubricating critical moving parts and checking for abnormal heat signatures. The task, completed in the early hours, ensured the vessel could maneuver safely into port without delay. This anecdote highlights not only the technical expertise required but also the commitment and readiness of LNG ship engineers to act whenever safety is at stake.
Regulatory and Classification Society Requirements
LNG ship maintenance is governed by a complex framework of international regulations and classification society rules. The International Maritime Organization (IMO) sets broad safety and operational standards, while classification societies such as Lloyd’s Register and DNV provide detailed technical requirements for machinery, hull integrity, and cargo systems. Compliance involves regular audits, documentation reviews, and physical inspections. Ships must maintain up-to-date records of all maintenance activities, including repairs, replacements, and system upgrades.
Studies indicate that a robust safety management system (SMS) is vital for ensuring ongoing compliance. This system integrates checklists, permits, and training records, creating a transparent trail for both internal and external review. Non-conformities, when identified, are addressed through corrective actions and follow-up inspections. The Chief Mechanic’s role is pivotal in coordinating these efforts, ensuring that every maintenance task aligns with regulatory expectations and supports the vessel’s operational certification.
Scheduled vs. Emergency Repairs: A Constant Balancing Act
While scheduled maintenance forms the foundation of LNG ship safety, emergency repairs are an unavoidable reality. The rate of emergency interventions can be influenced by factors such as equipment age, operational intensity, and environmental conditions. Research highlights that a proactive approach—using digital monitoring tools and predictive analytics—can reduce the frequency and severity of unplanned repairs.
Emergency repairs, though less frequent than scheduled tasks, often demand rapid assessment, resourcefulness, and clear communication. As the case study illustrates, the ability to mobilize a team for immediate action—whether for a leaking hose coupling or a failing fuel pump—can mean the difference between a minor disruption and a major safety incident. The Chief Mechanic’s leadership and the team’s preparedness are tested most during these high-pressure moments, reinforcing the critical role of maintenance as the unseen backbone of LNG ship safety.
When Things Go Sideways: Tales of Emergency Repairs and Rapid Response
Real-Life Breakdown: Fuel Pump Failure and Midnight Teamwork
On LNG vessels, the unexpected is never far away. One recent incident stands out—a sudden fuel pump failure in the middle of a night transit. The main engine’s power dropped sharply, and alarms echoed through the engine room. The Chief Mechanic and the engineering team were roused from their bunks, moving quickly but methodically. As documented in the case study, the immediate priority was to activate standby systems and keep the vessel safely underway while isolating the faulty pump. The team’s technical proficiency and calm under pressure made the difference. Within four hours, the damaged unit was replaced, and full propulsion was restored, averting a costly delay and maintaining the vessel’s safety margin.
The Anatomy of an Emergency Repair: From Klaxon to Fix
Emergency repairs on LNG carriers follow a well-rehearsed sequence. When the klaxon sounds, it’s not just about fixing a broken part—it’s about managing risk, time, and teamwork. The process begins with a rapid assessment: What failed? What systems are affected? The Chief Mechanic leads the diagnosis, drawing on both experience and real-time data. Safety protocols are non-negotiable; isolating the affected component and securing the area come before any hands-on work. Only then does the team move in, tools in hand, guided by checklists and clear communication.
Research shows that the effectiveness of these emergency interventions relies heavily on preparation. Preventative maintenance and regular drills ensure that everyone knows their role. As the case study highlights, “the consistent application of established procedures and continuous vigilance are essential for maintaining the safety and efficiency of the vessel.” Documentation is meticulous, not just for compliance, but to capture lessons learned for future incidents.
The Human Side—Team Nerves, Caffeine, and a Bit of Luck
Behind every successful emergency repair is a team working under pressure. The human element is as critical as any technical skill. During the fuel pump incident, nerves were tested. There’s a rhythm to these moments—quiet urgency, focused conversation, and the ever-present hum of machinery. Caffeine helps, but so does trust: trust in protocols, in each other, and in the leadership of the Chief Mechanic.
The case study notes that team morale is shaped by recognition, open communication, and shared experience. After the repair, a debrief brings everyone together to review what went well and what could be improved. Sometimes, a bit of luck plays its part—an easily accessible spare part, a quick diagnosis—but it’s the team’s preparation and adaptability that turn luck into success.
Trends in Root Causes of Emergency Repairs
Patterns emerge over time. Most emergency repairs stem from a handful of recurring issues: component fatigue, sensor failures, and the unpredictable effects of harsh marine environments. Studies indicate that integrating predictive maintenance tools and condition-based monitoring can reduce the frequency of such incidents. The case study recommends “implementing advanced predictive maintenance systems” to further minimize unplanned breakdowns.
While technology is advancing, the core lesson remains: even the best systems need skilled people ready to respond when things go sideways. The Chief Mechanic’s chair is where preparation, leadership, and teamwork meet the unpredictable reality of LNG ship operations.
Preventative Maintenance and Upkeep: Why Boring is Brilliant
The Unsung Power of Routine: Why the Best Days Are Uneventful
In LNG ship operations, the most successful days often pass without incident or excitement. This “boring” routine is not a sign of complacency, but rather the result of diligent preventative maintenance and a disciplined approach to upkeep. The Chief Mechanic’s daily oversight—scheduling inspections, monitoring system health, and ensuring compliance with safety protocols—creates a stable environment where surprises are rare. As noted in the case study, “consistent application of established procedures and continuous vigilance are essential for maintaining the safety and efficiency of the vessel.” Routine tasks like lubrication, filter changes, and system checks may seem mundane, but they are the backbone of operational reliability.
Research shows that preventative maintenance is critical for identifying issues before they escalate. Scheduled inspections and adherence to manufacturer guidelines extend equipment lifespan and reduce the risk of sudden failures. In LNG shipping, where the stakes are high and the cargo volatile, this approach is not just best practice—it is essential. The Chief Mechanic’s leadership in enforcing these routines ensures that the engineering team remains focused, prepared, and aligned with safety standards.
Case Study: How Predictive Maintenance Saved Us from a Major Engine Failure
A recent incident aboard an LNG carrier highlights the value of moving beyond traditional maintenance to embrace predictive technologies. During a routine transit, the vessel experienced a sudden drop in propulsion power. Thanks to the integration of predictive maintenance tools, the engineering team had already been monitoring subtle anomalies in the main engine’s fuel supply system. Real-time sensor data flagged irregularities in fuel pump performance, prompting the Chief Mechanic to schedule a targeted inspection.
When the failure occurred, the team was prepared. Standby systems were activated, and the faulty pump was quickly isolated. The Chief Mechanic led the team in a swift replacement operation, restoring full propulsion within hours. This rapid response minimized operational delays and prevented further complications. The case study notes, “This rapid intervention restored full propulsion power within four hours, minimizing operational delays and preventing further complications.” Without predictive maintenance and the discipline of routine monitoring, the outcome could have been far more disruptive.
The lesson is clear: predictive maintenance, supported by digital tools and real-time data, empowers teams to act before minor issues become major crises. It also reinforces the importance of cross-training, as team members familiar with critical systems can respond flexibly in emergencies.
Key Metrics: Unplanned Downtime Before and After Tech Upgrades
The shift from reactive to predictive maintenance has produced measurable improvements in operational efficiency. Studies indicate that integrating cloud-based maintenance software and real-time monitoring can reduce unplanned downtime by up to 20% within the first year. The Chief Mechanic’s department tracks several key performance indicators, including hours of unscheduled maintenance per voyage and the number of overdue maintenance tasks.
The case study emphasizes, “These metrics directly reflect the impact of predictive maintenance and enhanced planning on the vessel’s operational readiness and cost-effectiveness.” Regular analysis of these figures provides objective feedback on the effectiveness of new technologies and maintenance strategies. It also supports ongoing dialogue with executive leadership, ensuring that resource allocation aligns with operational needs.
Ultimately, the brilliance of preventative maintenance lies in its ability to make “boring” the new standard for excellence. By prioritizing routine, leveraging predictive tools, and tracking key metrics, LNG ship operations can achieve both safety and efficiency—often without fanfare, but always with purpose.
From Toolbox Talks to Team Triumph: Leadership and Morale at Sea
Experimenting with Recognition: Handing Out ‘MVP of the Month’
Recognition is a powerful motivator, especially in the close quarters of an LNG vessel. The Chief Mechanic’s team recently piloted a ‘MVP of the Month’ initiative, aiming to highlight exceptional contributions and boost morale. Each month, crew members nominate a peer who has demonstrated outstanding technical skill, teamwork, or a positive attitude during challenging operations. The winner is announced during a weekly toolbox talk, receiving a small token of appreciation and, perhaps more importantly, public acknowledgment from both peers and leadership.
Research shows that structured recognition programs can increase job satisfaction and reduce turnover in high-stress environments. Onboard, the effects are visible: increased engagement during daily briefings, more proactive problem-solving, and a subtle but noticeable lift in team spirit. As one engineer put it,
“It’s not about the prize—it’s about knowing your work matters to the team.”
Tackling Fatigue—Planned Shore Leave and Its Impact
Fatigue is a constant challenge in maritime operations, especially on LNG carriers where safety and precision are non-negotiable. The Chief Mechanic’s approach includes strict adherence to planned shore leave schedules, ensuring that all team members get regular opportunities to rest and recharge. Studies indicate that effective fatigue management not only improves safety but also enhances operational efficiency and decision-making.
Feedback from the latest crew survey suggests that shore leave is one of the most valued aspects of the job. Crew members report feeling more focused and less irritable after time ashore, with one respondent noting,
“A few days off the ship makes all the difference when you’re back in the engine room.”
While operational demands sometimes require flexibility, leadership prioritizes rest wherever possible, understanding its direct link to both morale and performance.
Wild Card: Hypothetical ‘No-Captain’ Day—Would the Ship Run as Smoothly?
During a recent team-building session, the Chief Mechanic posed a provocative question: what if the ship operated for a day without the Captain’s direct oversight? The exercise was designed to spark discussion about autonomy, trust, and the distribution of leadership responsibilities. Most crew members agreed that while routine tasks would likely continue smoothly, the absence of clear authority could create uncertainty during unexpected events or emergencies.
This thought experiment highlighted the importance of both formal leadership and empowered teams. It also underscored the value of cross-training and open communication—qualities that help the crew adapt quickly when leadership is temporarily unavailable. As the Chief Mechanic observed,
“A strong team doesn’t just follow orders—they anticipate needs and support each other, no matter who’s on the bridge.”
Surprising Morale Metrics from Our Last Crew Survey
Regular crew surveys provide valuable insights into team morale and areas for improvement. The most recent results were encouraging: over 85% of respondents described their work environment as supportive, and a similar percentage felt their contributions were recognized by leadership. Interestingly, the survey also revealed that opportunities for skill development and clear communication about operational changes were just as important to morale as traditional incentives like bonuses or time off.
These findings align with broader industry research, which emphasizes the role of professional growth and transparent leadership in maintaining high morale at sea. The Chief Mechanic’s ongoing efforts to foster open dialogue, recognize achievements, and prioritize crew welfare continue to shape a resilient and high-performing team—one that’s prepared for both routine operations and unexpected challenges.
The New Wave: Smart Tech, Process Tweaks, and a Safer, Leaner Future
The landscape of LNG ship maintenance is changing rapidly, shaped by the integration of smart technologies and a growing focus on efficiency and safety. Research shows that the adoption of digital tools like condition-based monitoring and artificial intelligence is no longer a distant vision—it’s becoming the new standard onboard. These advancements are not just about staying current; they are about transforming the way teams approach daily operations, problem-solving, and long-term planning.
Condition-based monitoring, for example, is now a reality on many LNG vessels. By using real-time data from sensors embedded in critical machinery, engineering teams can predict when maintenance is needed, rather than relying on fixed schedules or waiting for something to break. This shift allows for targeted interventions, reducing both unplanned downtime and unnecessary repairs. As highlighted in the case study, “Integrating a cloud-based system to analyze sensor data from critical machinery, forecasting potential failures and enabling condition-based maintenance…minimizes unplanned downtime and optimizes resource allocation.” The result is a leaner, more proactive approach to vessel upkeep.
Non-destructive testing (NDT) has also become a cornerstone of modern LNG ship maintenance. Techniques such as ultrasonic testing, magnetic particle inspection, and advanced visual tools allow teams to spot signs of wear, corrosion, or fatigue before they escalate into costly or dangerous failures. Studies indicate that early detection through NDT not only extends the lifespan of equipment but also supports compliance with stringent safety regulations. This is especially vital in LNG operations, where even minor leaks or mechanical issues can have significant consequences.
Another area seeing significant improvement is material procurement. Traditionally, waiting for spare parts could mean extended delays, increased costs, and operational headaches. Today, digital inventory management systems and automated reordering processes are streamlining this aspect of shipboard life. As the case study recommends, “Develop an automated system for tracking spare parts, triggering reorders based on consumption rates and lead times. This reduces stockouts and expedites repair processes.” The impact is clear: less waiting, faster repairs, and improved readiness for both routine and emergency maintenance.
Comparing legacy procedures to today’s tech-driven workflows, the difference is striking. Where once teams relied on manual logs, paper checklists, and reactive repairs, they now benefit from interconnected systems, real-time analytics, and predictive insights. This transition is not without its challenges—adapting to new tools and processes requires ongoing training and a willingness to embrace change. Yet, the gains in safety, efficiency, and morale are undeniable.
Ultimately, the new wave of smart technology and process refinement is shaping a safer, more resilient future for LNG maritime operations. The Chief Mechanic’s evolving role—balancing technical expertise, leadership, and adaptability—remains central to this transformation. As digital solutions become further embedded in daily routines, teams are better equipped to anticipate problems, respond swiftly to emergencies, and maintain the highest standards of safety and compliance.
Looking ahead, continuous improvement will depend on both technological innovation and human development. Investing in advanced training, fostering a proactive safety culture, and ensuring open communication between ship and shore will be key. As the industry moves forward, the lessons learned from the Chief Mechanic’s chair—embracing smart tech, refining processes, and prioritizing safety—will continue to drive operational excellence across the LNG fleet.
TL;DR: If you want to know what keeps LNG ships—and their crews—safe, moving, and motivated, it boils down to meticulous maintenance, clear-eyed leadership, and never underestimating the power of your people. Technology helps, but teamwork seals the deal.
Comments
Post a Comment