Picture this: You're 150 nautical miles from the nearest coastline, and a critical pump—one you thought would hold—gives out in the middle of the night. The hum of a well-oiled machine is gone, replaced by stress and the frantic sounds of troubleshooting. This isn’t just the stuff of nightmares for marine engineers—it's been the standard operating risk for generations. But here's the twist: maintenance doesn't have to be reactive, filled with dread and sleepless nights. Thanks to the evolution of the Planned Maintenance System (PMS), ships now run not just on diesel and steel, but on knowledge, foresight, and the quiet triumph of compliance. Grab your mental notepad—let’s navigate how PMS transformed the maritime world, and why the stakes have never been higher.
From Grease-Stained Logbooks to Digital Command Centers: The Evolution of Ship Maintenance
Ship maintenance has come a long way since the days when marine engineers relied on grease-stained logbooks and handwritten charts. In the 1960s, maintenance was a reactive process—crews patched up machinery only after it failed, recording repairs in paper registers (Banham & J.W., 1963). These manual records were not only prone to error but also made it difficult to track trends, schedule preventive tasks, or ensure compliance with growing regulatory demands.
The limitations of paper-based systems became clear as ships grew more complex and the cost of unplanned downtime increased. Early maintenance management was about fixing what broke, not preventing breakdowns in the first place. This approach often led to unpredictable repairs, higher costs, and increased safety risks. As technology advanced, the industry began to shift toward more systematic and proactive strategies.
The introduction of Computerized Maintenance Management Systems (CMMS) marked a turning point. By the late 20th century, these digital tools allowed marine engineers to store, retrieve, and analyze maintenance data more efficiently. Planned Maintenance System (PMS) software soon followed, enabling scheduled inspections, proactive replacements, and detailed documentation—all essential for modern ship maintenance and regulatory compliance (Cao et al., 2017).
Today, digital PMS platforms are mainstream, offering real-time maintenance scheduling, documentation, and inventory management. These cloud-based systems not only reduce the risk of human error but also improve transparency and operational efficiency. Research shows that digital PMS solutions allow for seamless integration with inventory control, safety management, and regulatory compliance frameworks (Park et al., 2012; Starr & Ball, 2000). This holistic approach means that maintenance is no longer just about repairs—it’s about managing the entire lifecycle of shipboard assets.
Modern marine engineering is as much about data and documentation as it is about torque wrenches. As one industry insight puts it:
'Modern marine engineering is as much about data and documentation as it is about torque wrenches.' — Based on insights by Cao et al.
With digital PMS platforms, marine engineers can now access maintenance records from anywhere, coordinate with shore-based teams, and ensure that every action is logged and auditable. The transition from paper to digital has fundamentally reshaped how maintenance is planned, executed, and reviewed—making it a cornerstone of safe, efficient, and compliant ship operations.
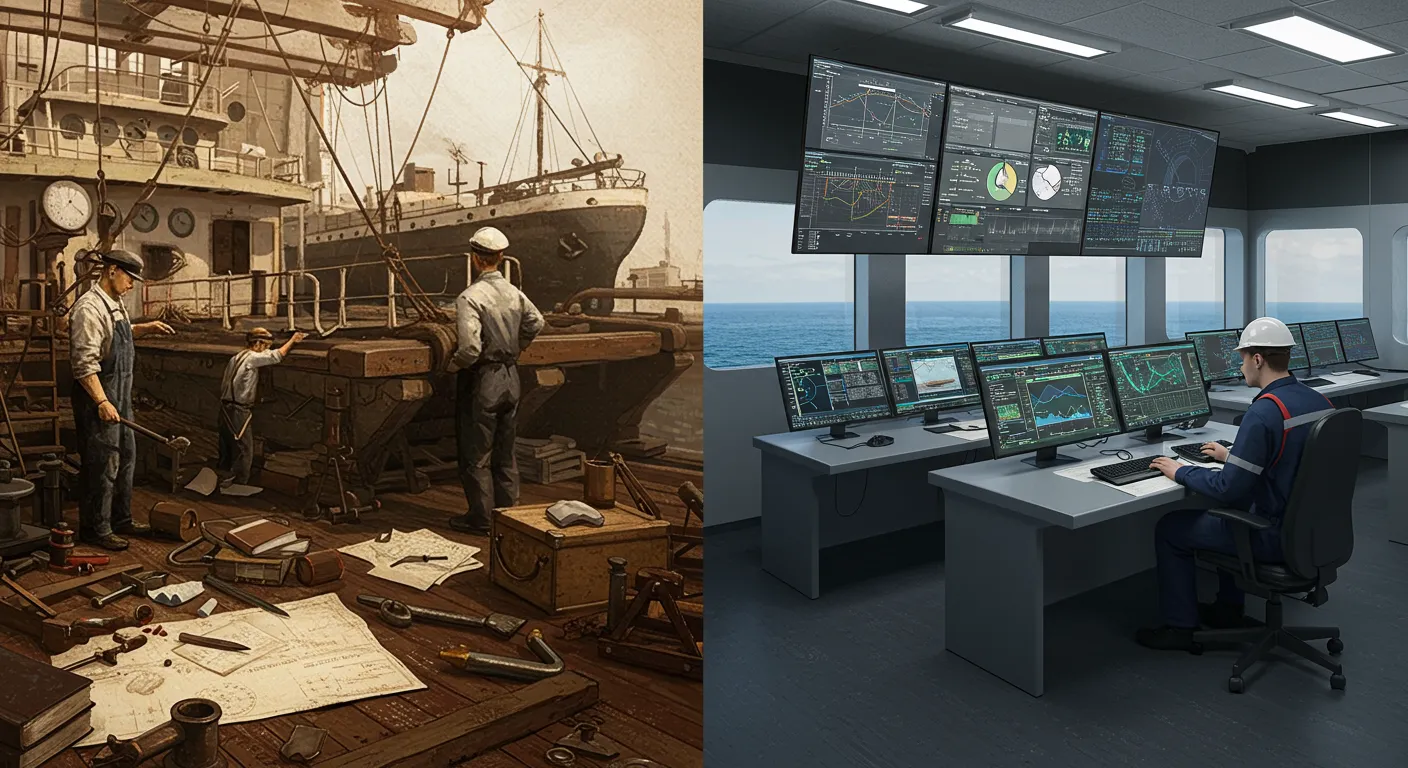
Avoiding Nightmares: How PMS Software Rewires Risk and Reliability at Sea
In the world of marine engineering, the difference between smooth sailing and a costly disaster often comes down to maintenance strategy. Historically, many vessels relied on reactive maintenance—waiting for something to break before fixing it. This approach, while simple, frequently led to unpredictable downtime, spiraling repair costs, and heightened risk of maritime accidents. As ship systems became more complex, the consequences of a sudden failure—like a main pump breakdown at sea—could escalate rapidly, threatening not just finances but the very Safety of Life at Sea.
Research shows that a Planned Maintenance System (PMS) fundamentally changes this equation. By enabling scheduled inspections and proactive replacements, PMS software helps marine engineers address issues before they become emergencies. Instead of scrambling to fix a critical failure at 2 a.m., crews can rely on a structured maintenance plan. As one industry expert put it,
'A good PMS won’t call you at 2 a.m.—because nothing has failed.' — Paraphrased from Doherty, 2016
Beyond operational convenience, PMS is now a regulatory necessity. The International Safety Management (ISM) Code and SOLAS require vessels to maintain detailed maintenance records and demonstrate compliance during inspections. Failing to provide adequate documentation can result in fines, detentions, or even the loss of certification—outcomes no operator wants to face. Studies indicate that PMS documentation is essential for passing Port State Control inspections and satisfying classification societies’ requirements (Nichols & Khan, 2015; Svilicic et al., 2019).
One of the most valuable features of modern PMS software is its ability to support systematic risk management. By identifying and prioritizing high-risk components, PMS allows engineers to focus attention where it matters most. Audit trails and maintenance histories transform what could be a chaotic engine room into a model of order, supporting root cause analysis and continuous improvement (Almeida & Rodrigues, 2019). This structured approach not only minimizes the risk of catastrophic failures but also streamlines knowledge transfer between crew members, ensuring operational consistency even during personnel changes.
Data from Ettaye et al. (2018) highlights that breakdown maintenance often results in higher repair costs and secondary damages. In contrast, PMS-driven preventive and predictive strategies reduce both costs and operational unpredictability. For international operations, ISM Code compliance is non-negotiable—making PMS not just a best practice, but a baseline requirement for safe, reliable, and legally compliant shipping.
The Anatomy of Maintenance: From Reactive Wrenches to Predictive Sensors
Marine engineering has seen a significant shift in maintenance strategies over the decades. The journey began with breakdown, or corrective, maintenance—a reactive approach where repairs only happened after equipment failed. This method, while straightforward, often led to costly downtime, secondary damages, and increased stress for engineering teams. As research shows, breakdown maintenance can result in cascading failures and expensive emergency interventions (Ettaye et al., 2018).
To address these challenges, the industry moved towards preventive maintenance. This strategy schedules interventions based on time or operational hours, aiming to prevent failures before they occur. While preventive maintenance is a step up from reactive methods, it is not flawless. Scheduled tasks may still be unnecessary if equipment is in good condition, leading to wasted resources and potential over-maintenance.
The latest evolution is predictive—or condition-based—maintenance. This approach leverages real-time data from sensors that monitor vibration, temperature, and fluid conditions. By analyzing these parameters, marine engineers can anticipate when a component, such as a pump bearing, is likely to fail. For example, vibration sensors can detect subtle changes in a pump’s operation, allowing for targeted interventions before a breakdown occurs. As von Enzberg et al. note, “Condition monitoring isn’t fortune-telling—it’s about using what you know now to avoid what you don’t want tomorrow.”
Modern Computerized Maintenance Management Systems (CMMS) and digital Planned Maintenance Systems (PMS) integrate all these maintenance strategies. These platforms allow marine engineers to tailor their approach based on machinery criticality, cost, and available technology. A PMS can coordinate preventive, predictive, and corrective actions, ensuring that maintenance is both timely and efficient. Integration with inventory management further ensures that spare parts are available when needed, reducing delays and controlling costs.
Feature | Benefit |
---|---|
Real-time sensor monitoring (vibration, temperature, fluids) | Enables early detection of equipment issues |
Condition-based maintenance | Reduces unnecessary interventions, saving money |
Inventory integration | Ensures necessary spare parts are on hand |
Studies indicate that the shift towards predictive and condition-based maintenance is transforming marine operations. By combining proactive and reactive approaches within a unified PMS, engineers can stay one step ahead—improving reliability, safety, and cost-effectiveness across the fleet.
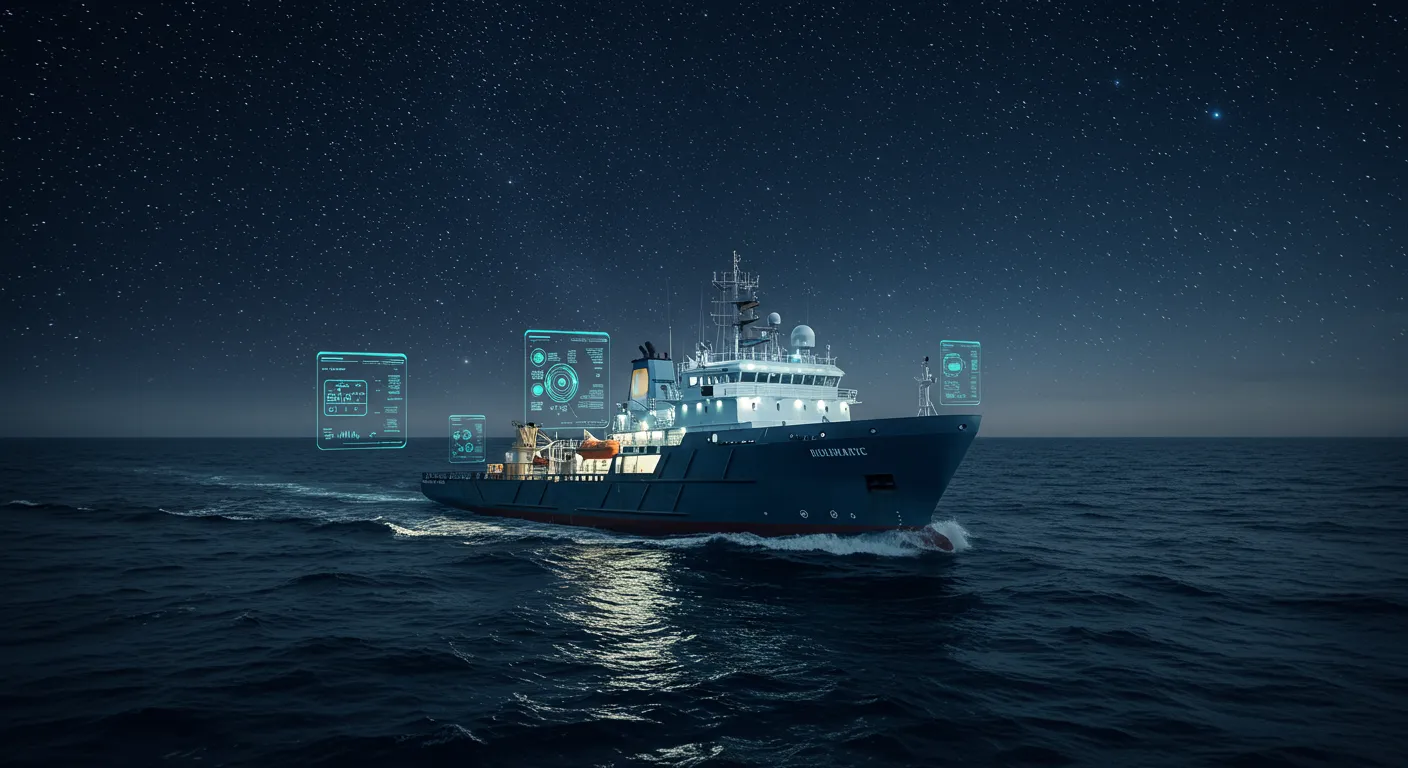
Making It Work: The Messy Reality of PMS Implementation
PMS implementation is rarely a smooth, one-size-fits-all journey. While the promise of streamlined maintenance and airtight documentation is appealing, the reality for marine engineers is often far more complex. The process begins with selecting the right system—an essential step, since not all PMS software is created equal. Customization is key; research shows that a PMS must be tailored to each vessel’s unique machinery, operational profile, and regulatory requirements. Generic templates simply don’t cut it, and manufacturer documentation is crucial for ensuring accurate system setup (Popescu et al., 2018).
Once a system is chosen, the next hurdle is data migration. Migrating information from old logbooks or basic software into a new PMS demands meticulous attention to detail. Errors at this stage can lead to gaps in maintenance documentation, which may compromise compliance or operational safety. Studies indicate that data integrity is a persistent maintenance system challenge, especially when dealing with legacy records and diverse equipment types.
Yet, even the most advanced PMS can falter without crew buy-in. Crew training is often the make-or-break factor in successful PMS implementation. As Doherty (2016) aptly summarized,
'Installing PMS software is easy. Changing minds? That’s the real marathon.'
Resistance to change is common, particularly when transitioning from familiar manual routines to digital workflows. Effective training programs, ongoing support, and clear communication are essential for transforming skeptics into advocates. Research underscores that continuous engagement and capacity building help crews adapt to new maintenance documentation practices and leverage system features fully.
Once operational, a well-configured PMS becomes the backbone of daily maintenance. It centralizes checklists, task assignments, and resource management—enabling marine engineers to prioritize work, allocate spare parts, and document interventions in real time. This not only streamlines audits and compliance checks but also supports knowledge transfer during crew changes, ensuring continuity and operational consistency.
Despite these benefits, PMS implementation is not without its challenges. Integration complexity, adapting to emerging technologies, and maintaining data quality are ongoing concerns. The process typically unfolds in phases: system selection, data migration, crew training, and ongoing support. Each stage demands attention to detail, collaboration, and a willingness to adapt as new technologies and regulations emerge.
Ultimately, making PMS work on board is less about the software itself and more about people, processes, and persistence. The journey from initial setup to daily use is rarely linear, but with the right approach, marine engineers can transform maintenance from a reactive burden into a proactive asset.
The Human Web: Why Crew Collaboration and Inventory Management Matter
Behind every effective Planned Maintenance System (PMS) lies a network of people—engineers, bridge officers, and shore-based teams—whose collaboration shapes the system’s real-world impact. No matter how advanced the technology, a PMS is only as good as the crew working together to keep it running smoothly. In marine engineering, this human web is essential for translating digital plans into safe, efficient operations.
Modern PMS platforms do more than just schedule tasks. They act as hubs for communication, knowledge sharing, and resource allocation. When engineer and bridge teams coordinate using a PMS, daily maintenance becomes a shared responsibility rather than an isolated chore. Research shows that digital PMS solutions, especially those with mobile app capabilities, have transformed how knowledge is transferred during crew rotations. Instead of relying on handwritten notes or memory, outgoing crew can log detailed maintenance records, attach photos, and flag issues for incoming teams—making handovers less stressful and more reliable (Doherty, 2016; Cao et al., 2017).
Inventory management is another critical piece of this puzzle. Integrated inventory modules within PMS platforms track spare parts, monitor usage, and trigger procurement when stocks run low (Samaranayake & Kiridena, 2012). This means no more frantic calls for missing parts or last-minute improvisation. Instead, engineers can focus on planned tasks, confident that the right spares are available when needed. As one veteran chief engineer puts it:
"You don’t get extra points for firefighting if it was preventable in the first place."
Daily task assignments, supported by real-time feedback loops, drive continuous improvement. Crew members can update maintenance records directly from the field, thanks to PMS mobile apps. These tools allow engineers to log running hours, upload photos, and submit spare parts requisitions—even when the vessel is far from port. Studies indicate that this real-time documentation supports both condition-based and corrective maintenance, reducing the risk of oversight and ensuring compliance with international standards.
Ultimately, the success of a PMS depends on the people who use it. Effective communication, clear task delegation, and shared access to up-to-date maintenance records form the backbone of operational reliability. As digital platforms continue to evolve, the integration of inventory management and mobile accessibility will only deepen the value of crew collaboration, making shipboard maintenance smarter, safer, and more connected than ever before.
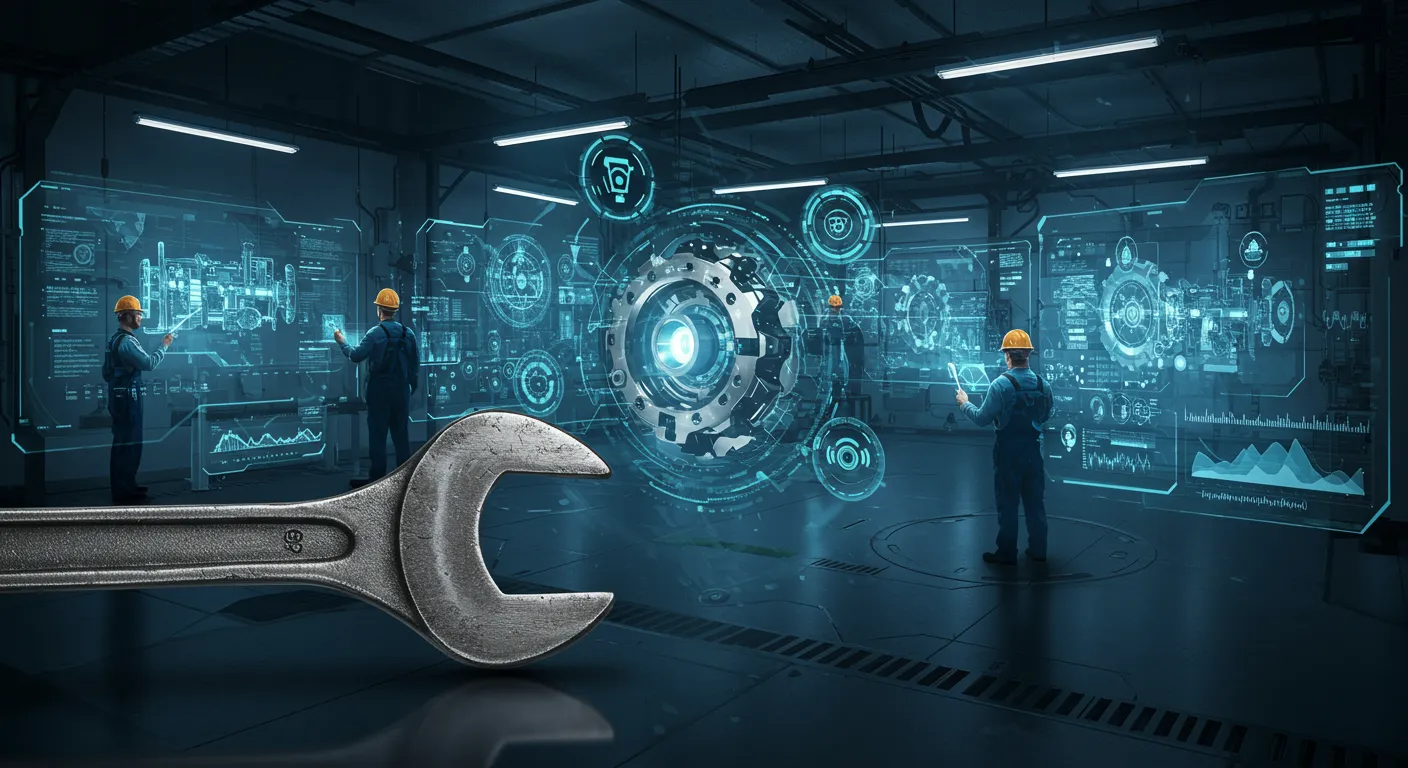
No Crystal Balls… Just Data: The Future of PMS, AI, and the ‘Smart Ship’
For marine engineers, the days of relying on intuition or waiting for something to break are fading fast. The future of maintenance lies in data-driven systems—no magic required. Today’s Computerized Maintenance Management Systems (CMMS) are rapidly evolving, shaped by trends like Artificial Intelligence, cloud-based PMS solutions, and mobile-first solutions. These advances are not just buzzwords; they are fundamentally changing how ships are maintained and operated.
Machine learning and predictive analytics now allow ships to spot trouble before it happens. By analyzing sensor data—such as vibration, temperature, or oil quality—AI-driven systems can detect patterns that signal early signs of equipment wear or failure. As Chornous & Gura (2020) highlight, this means maintenance can be scheduled before breakdowns strike, reducing both downtime and costs. In the words of one industry outlook,
'You can’t stop every breakdown, but you can make them vanishingly rare.'
Cloud-based PMS solutions are another game changer. These platforms connect ship and shore operations in real time, enabling seamless data sharing and collaboration. Research shows that cloud and mobile connectivity not only reduce the IT burden onboard (Cao et al., 2017), but also ensure that maintenance records, inventory levels, and compliance documentation are always up to date and accessible from anywhere. Mobile-first solutions empower crew members to log maintenance activities, upload photos, and access checklists using handheld devices, streamlining day-to-day operations and supporting condition-based maintenance strategies.
Regulatory compliance, once a source of stress for marine engineers, is also being transformed by digital systems. Advanced PMS platforms can automatically generate audit-ready documentation, making regulatory reporting routine rather than a dreaded surprise (Svilicic et al., 2019). Audit readiness is improved, and the risk of missing critical inspections is minimized.
Looking ahead, the potential for fully integrated digital ecosystems is emerging. Imagine a future where PMS, safety management, and automation platforms converge—creating a smart ship environment where every system communicates and collaborates. Predictive analytics will enhance equipment uptime, reduce lifecycle costs, and support sustainability goals. Studies indicate that these CMMS future trends are less science fiction and more a practical response to the growing complexity of shipboard operations.
For marine engineers, embracing these technologies means shifting from reactive to proactive maintenance. The focus is on using data—not guesswork—to guide decisions, improve safety, and ensure compliance. The future of ship maintenance is smart, connected, and powered by information.
Conclusion: The Art of Staying Afloat—It’s More Than Just Following Checklists
Maritime maintenance has evolved far beyond the days of paper logs and reactive repairs. Today, the Planned Maintenance System (PMS) stands at the center of ship maintenance, not simply as a digital tool, but as a foundation for a proactive, resilient culture. Research shows that the most effective marine engineers do not just follow checklists—they use PMS to anticipate challenges, prevent failures, and drive continuous improvement across every aspect of vessel operations.
True mastery in maritime maintenance comes from foresight. The best marine teams understand that compliance is only the starting point. By leveraging PMS for real-time updates, meticulous data entry, and ongoing crew training, they create an environment where information flows freely and decisions are based on accurate, up-to-date records. This approach supports not only regulatory requirements, such as those set by the ISM Code and SOLAS, but also the broader goals of operational efficiency and safety.
Success in ship maintenance is not achieved in isolation. It relies on open communication between departments, relentless attention to data quality, and a shared commitment to improvement. As Doherty (2016) notes, culture change is at the heart of effective planned maintenance. When marine engineers and crew embrace the PMS as a living system—one that adapts to new technologies, evolving risks, and changing regulations—they enable the vessel to remain agile and compliant in a complex maritime environment.
The shift from a ‘fix’ mentality to a ‘prevent’ mindset is essential for maritime safety and sustainability. Predictive maintenance, enabled by digital PMS platforms, allows teams to act before problems escalate, reducing downtime and protecting both assets and personnel. As digital and AI-powered solutions continue to advance, the opportunities for smarter, more integrated maritime maintenance will only grow.
‘Maintenance excellence isn’t about the absence of breakdowns, but the presence of resilience.’ — Reflecting the spirit of best-in-class marine teams
In the end, the art of staying afloat is not about ticking boxes or meeting the bare minimum. It is about building a culture where continuous improvement, collaboration, and strategic use of technology come together to reshape ship maintenance. The future of maritime maintenance belongs to those who see PMS not just as a system, but as a catalyst for resilience and proactive ship management.
TL;DR: Marine engineers today stand at the frontier of proactive, technology-driven ship maintenance. With a well-implemented PMS, they ensure safety, reliability, and regulatory adherence—no more nightmares of mid-sea breakdowns, just the steady hum of vessels running as they should.
Comments
Post a Comment